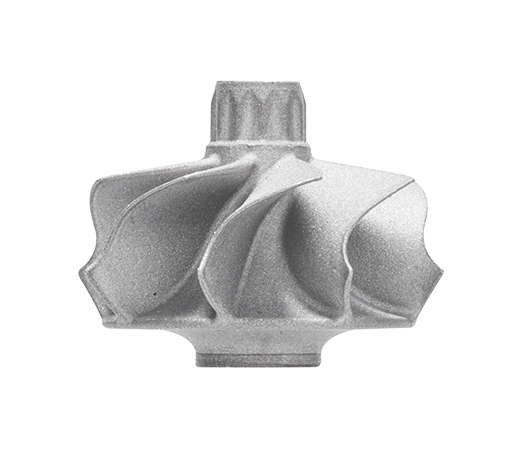
Vacuum investment casting
Ground tapping method
Highly productive melting and casting process for complex components made of highly heat-resistant materials. Large quantities can also be produced in a short period of time with a very high level of reproducibility.
- From individual parts to large series
- High degree of purity
- Possibility of targeted grain refinement on the castings
- High degree of automation
Tilting crucible method
Melting and casting process for the production of complex components made of high-temperature resistant materials with a high purity and very good reproducibility.
- From individual parts to large series
- Very high degree of purity
- High degree of automation in production, autonomous casting by casting cell (pre-heating to cooling)
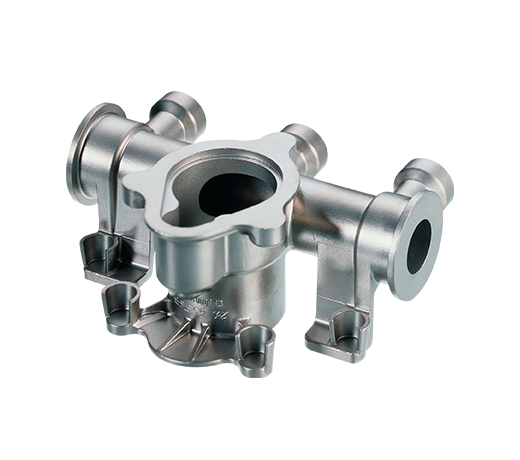
Open air investment casting
Conventional method
The conventional open investment casting - is a lost wax process that is characterised by an almost unlimited selection of alloys.
- Component weight up to 100 kg
- Manual pouring off of the casting cluster in an oxygenated environment
- The mould is filled manually via a ladle and is controlled by the casting speed
- Maximum installation space 600 x 600 x 550 mm
Roll-over technology
A very high material quality is achieved with roll-over technology. After melting the alloy, the furnace rotates 180 degrees in a few seconds. The mould shell that is flanged directly to the furnace is filled precisely and with low turbulence in the process, also while using inert gas.
- The influence of oxygen is eliminated by using an inert gas bell.
- The maximum installation space is 580 x 400 mm diameter
- Maximum casting weight of 100 kg
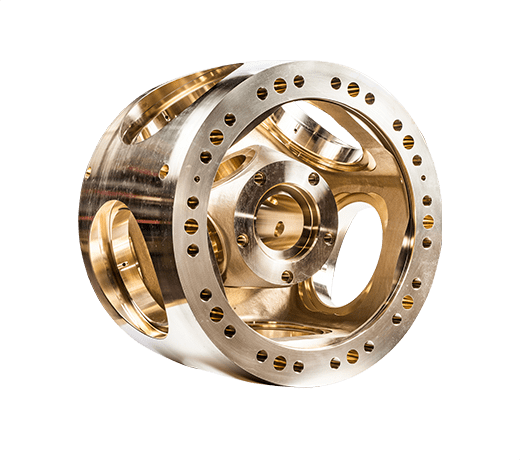
Sand casting
The sand casting process offers a high degree of freedom and the economic production of complex components with undercuts and cavities
- For individual parts and small series
- Production according to the permanent model, lost model or based on printed/milled moulded parts
- Part weights: Copper alloys up to 8,000 kg, steel alloys up to 2,500 kg
- Production using a lost mould
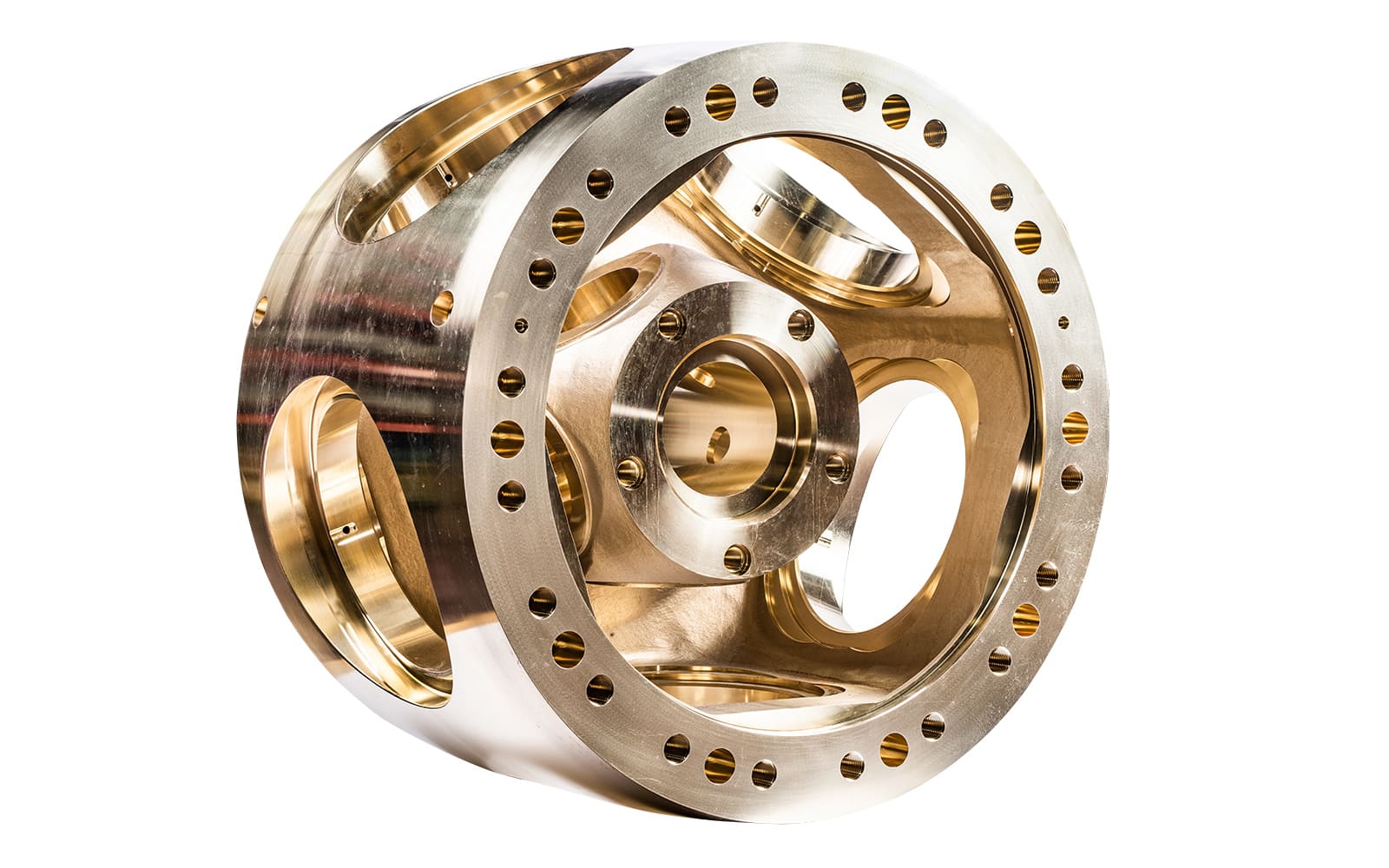
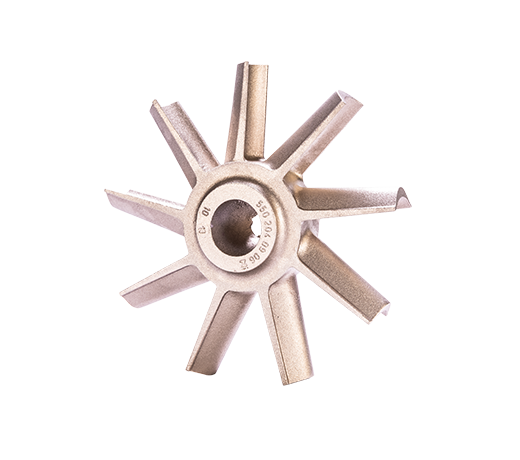
Croning casting / shell casting
Complex components with cavities and a high surface quality can be economically produced with Croning casting or shell casting.
- Surface quality Ra 6.3 µm
- Large series
- Metallic models
- Weight range up to about 20 kg
- Part dimensions up to about 400 x 250 x 200 mm
- Production using a lost mould
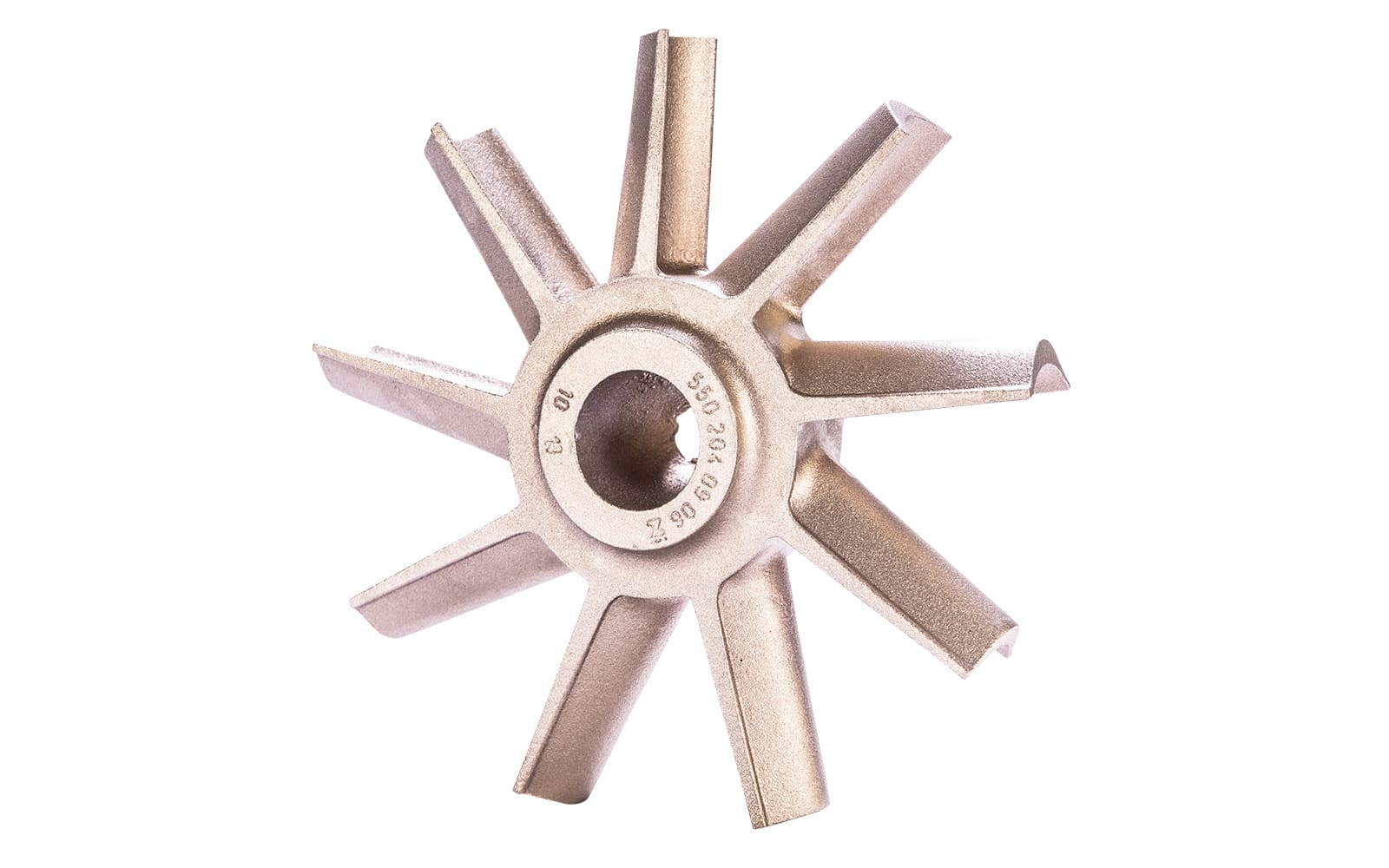
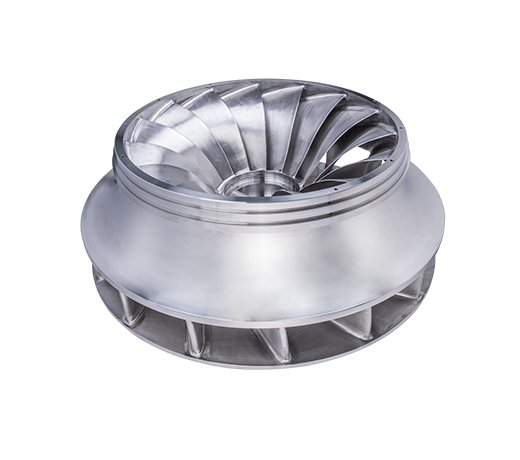

Direct Contact
P +49 (0) 7571 70 370
E zgm@zollern-nospam.com
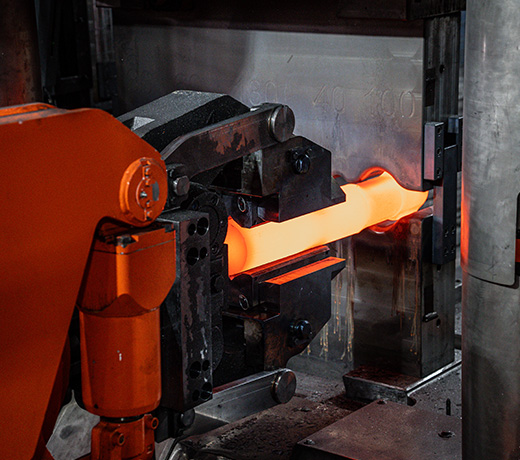
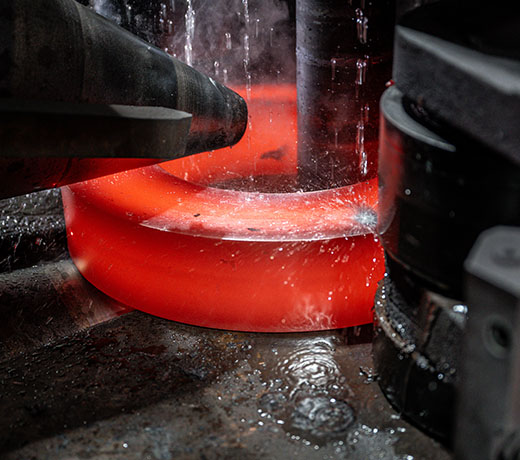
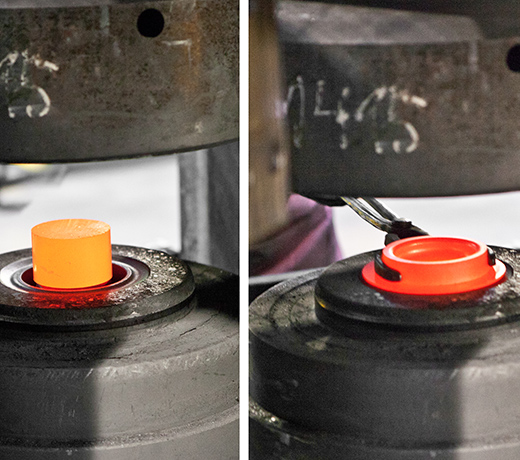
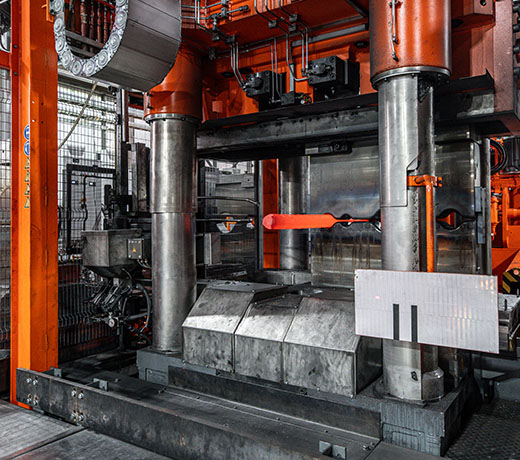
Process chain
ZOLLERN offers a high vertical range of manufacture for efficient processes and first-class quality.
- Master forming
- Metal forming
- Separating
- Changing material properties
- Machining
- Heat treatment
- NDT tests according to customer requirements (PT/UT/MT)
- Material testing (tensile test, notched bar impact test, hardness test, electrical conductivity)
- Metallographic examination (grain size determination, microstructure assessment, etc.)
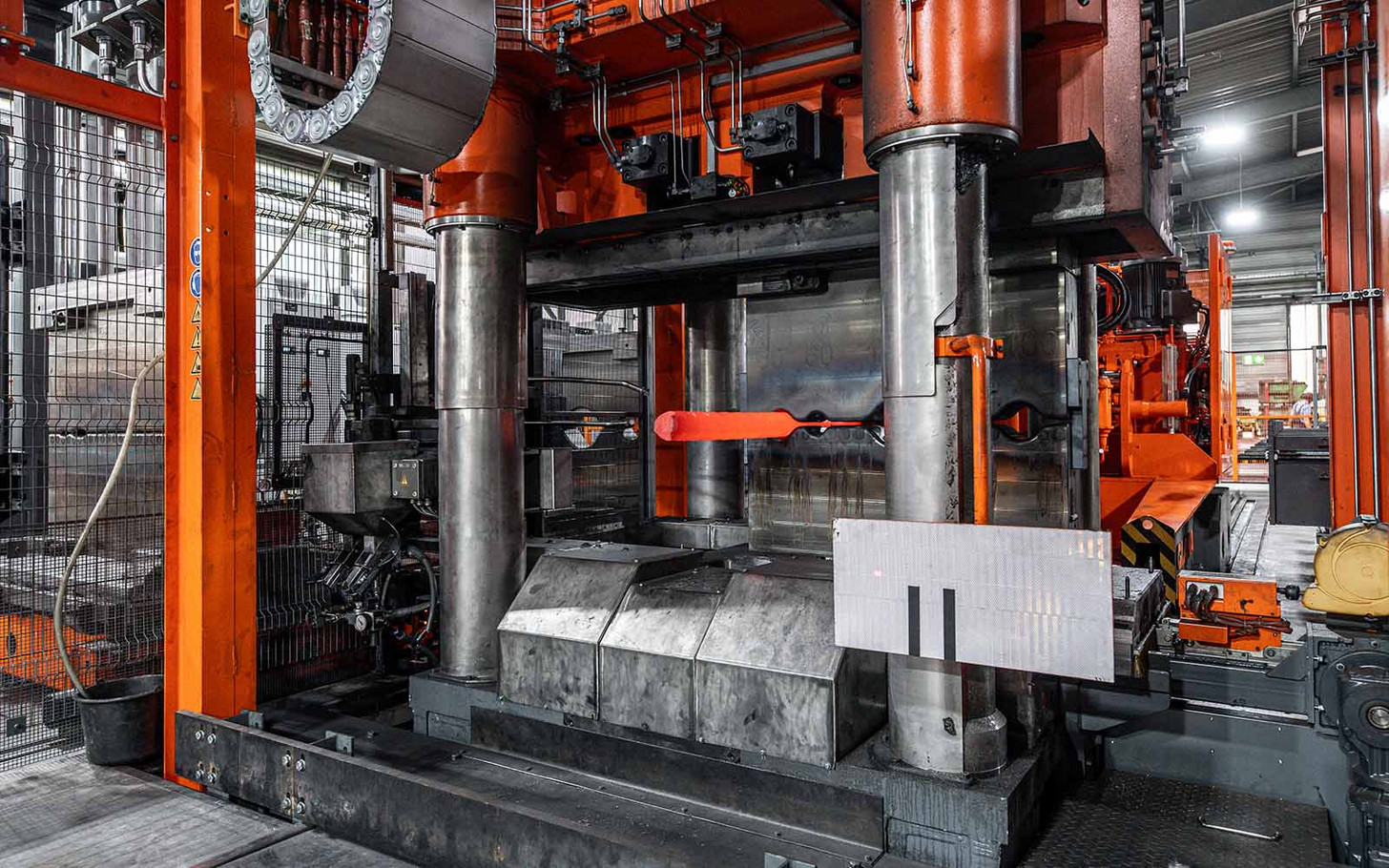
Direct Contact
P +49 (0) 7571 70 370
E zgm@zollern-nospam.com
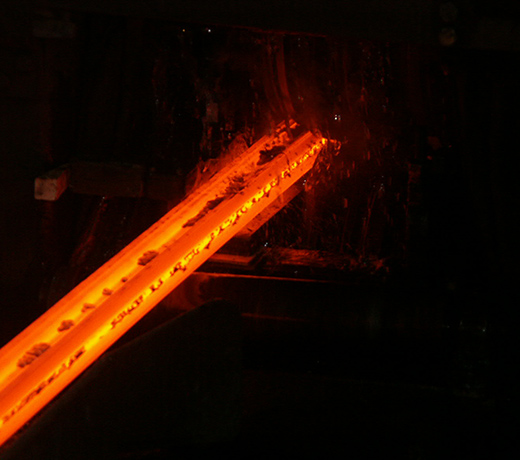
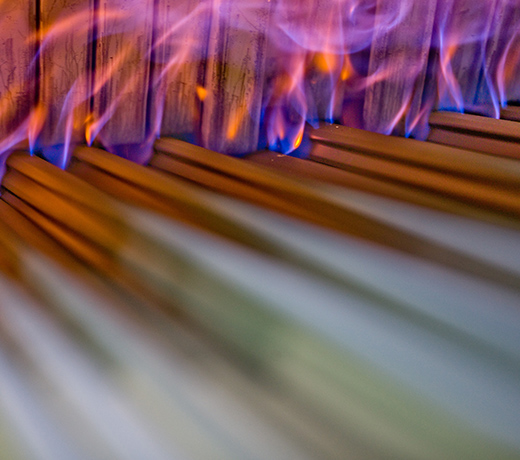
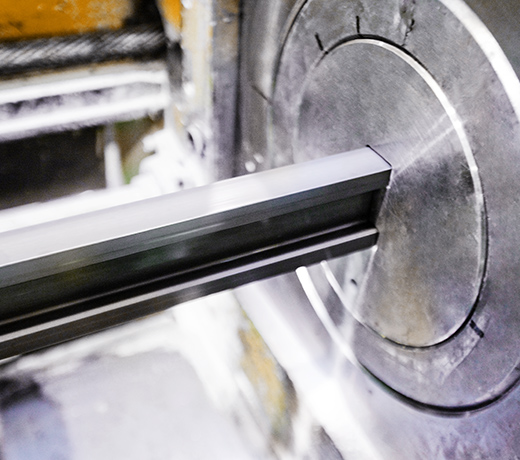

Cold rolling
With cold rolling, a wire rod is brought into the specified final contour at room temperature by rolling. Several rolling units in a production line automatically perform this process and give the profiles a high surface quality. The process is particularly well-suited for manufacturing small profile geometries, which are needed in larger quantities.
Direct Contact
P +49 (0) 7571 70-380
E zst@zollern-nospam.com